气泡是玻璃生产中常见的一种缺陷,超白玻璃相比普通玻璃,更容易在澄清区域出现气泡。
生产超白浮法玻璃时,存在的主要问题就是玻璃液澄清困难。
因为超白玻璃中铁含量低,导热系数较高,是普通玻璃的3~4倍,导致超白浮法玻璃的透热性好,玻璃液温度高,黏度低,在水平方向对流强度大,成形环流在澄清区停留时间短,使得玻璃液中残留的气泡来不及排出。
由于铁含量低,整个池深方向垂直温度梯度明显要比普通浮法玻璃小,池底温度比普通浮法玻璃高6%左右。
玻璃液的上下温差相对较小,使得对流减小,因此气泡排出比普通浮法玻璃更为困难。
另一方面,成形环流下方的回流玻璃液在前进过程中温度不断上升,使本已被玻璃液吸收的微气泡在热化学的作用下又被重新释放到玻璃液中。
同时低铁玻璃液黏度较低,微气泡极易升到表面流中,导致成形流玻璃液中气泡明显上升。
因为超白玻璃透热性好,池底温度高,水平方向对流强度大,对池底、池壁耐火材料侵蚀严重,因此耐火材料也容易在过程中形成气泡。
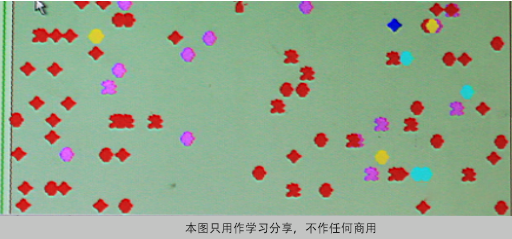
在保证熔化质量的前提下,适当降低澄清区玻璃液温度。通过降低末对小炉燃料用量来降低熔窑下游玻璃液的温度,实现降低熔窑澄清区池底玻璃液温度和减小玻璃液流动性的目的,减缓玻璃液对澄清区池底耐火材料的侵蚀作用。
将澄清区底部外层原来使用的硅钙板保温层拆除,并辅助通风措施降温,内层耐火材料的表面温度从200℃降低到50℃,达到降低玻璃液接触位置耐火材料温度的目的,从而达到降低界面温度、降低玻璃液的流动性、减缓玻璃液对澄清区池底耐火材料的侵蚀作用。
原来使用的卡脖水包压入深度为340mm,改为使用压入深度280mm卡脖水包,可减小熔窑玻璃液回流,降低玻璃液与耐火材料界面处的温度和流速,减缓玻璃液对澄清区池底耐火材料的侵蚀。
经过一系列调整后,实现了降低熔窑澄清区池底温度、降低玻璃液流动性的目的。玻璃液中气泡缺陷逐步减少,玻璃板带的质量逐步恢复到正常水平,并能长期保持稳定。
由于超白玻璃铁含量的降低,相对于普通白玻,在熔化过程中导热系数、黏度会有很大的不同,在生产过程中对应会产生池底温度升高、玻璃流动性明显增强等情况,对耐火材料侵蚀加剧,容易出现耐火材料侵蚀气泡。
在超白玻璃窑炉设计上,需要考虑玻璃液流动比较强、侵蚀比较严重的部位,对设计尺寸进行优化,使用更加耐受冲刷、抗侵蚀的耐火材料,并考虑降低这些部位的保温效果,减少耐火材料在运行过程中的侵蚀,避免产生气泡。
在熔化过程中,为了实现窑炉节能,通常会增加卡脖水包的压入深度,加强窑炉的保温,但是这些措施会影响玻璃液回流、对流,造成熔窑局部温度升高,增加熔窑耐火材料的局部侵蚀。
在超白玻璃生产过程中,需要综合考虑熔窑节能、窑炉保护和长期熔化质量稳定的平衡,才能实现长期高质量生产的目标。
原文始发于微信公众号(光伏产业通):超白浮法玻璃易现气泡缺陷的预防措施