光伏建筑是利用太阳能发电的一种新形式,通过将太阳能电池安装在建筑的围护结构外表面或直接取代围护结构外表面结构来提高发电。
国家对BIPV技术的政策扶持、价格补贴以及巨大发展空间及市场需求,使BIPV技术得到长足的发展,也将促使新封装材料及生产技术不断涌现,封装工艺和装备不断更新升级。
BIPV双玻组件封装材料主要有聚乙烯醇缩丁醛(PVB)及聚乙烯醋酸乙烯共聚物(EVA),
其化学结构如下:
使用PVB胶膜进行双玻组件封装,一般须在层压机上将电池片与玻璃固定,此时的组件样品不易冷却透明,需二次加热再冷却,故使用高压釜高温高压再次封装,取出后冷却速度缓慢。
PVB胶膜
整个封装流程复杂,操作繁琐,封装时间一般在一个小时以上,大大影响封装效率,另外,PVB树脂的价格比EVA树脂高,故使用PVB胶膜封装双玻太阳能组件存在成本较高且封装效率低等问题。
常规组件用EVA胶膜用于双玻组件封装时,易出现电池片或汇流带移位、组件边角气泡、缺胶等组件缺陷。
为克服上述封装材料的缺点,本文介绍一种既能解决常规EVA胶膜封装双玻组件时出现的组件缺陷问题,又能替代聚乙烯醇缩丁醛(PVB)胶膜以简化生产流程,提高生产效率,降低成本的封装材料—双玻组件用EVA胶膜的制备过程,同时将其与常规EVA胶膜及PVB胶膜进行封装工艺及效果对比分析。
EVA胶膜
-
双玻组件专用EVA胶膜的制备
将EVA树脂及功能树脂(鹿山新材合成)混合均匀,投入流延机中,调节模头使胶膜厚度在0.50±0.02mm范围内经冷却、牵引、收卷,得到双玻组件专用EVA胶膜。
具体制备流程图如下:
双玻组件专用EVA胶膜的制备流程
-
不同封装胶膜的层压封装实验
选用相同类型的钢化玻璃及太阳能电池片,采用钢化玻璃/胶膜/电池片/胶膜/钢化玻璃的叠层结构(如下图),分别将相同厚度的双玻组件专用EVA胶膜、常规组件用EVA胶膜、PVB胶膜制成叠层结构,设定层压机工艺进行同步层压,对比不同封装材料在层压机封装过程中的工艺适应性。
双玻光伏组件的叠层结构
-
EVA胶膜及PVB胶膜封装结果比较
表1为双玻组件专用EVA胶膜、常规组件用EVA胶膜及PVB胶膜三种封装材料在相同层压时间及压力,但不同层压温度下,用于双玻组件封装后的组件外观效果对比结果。
表1不同层压温度下,三种封装材料封装工艺适应性对比
从表1中可以看出,在不同层压工艺温度下,使用常规EVA胶膜封装双玻组件,均出现缺胶、气泡或移位现象;在层压机层压温度低于155℃时,使用PVB胶膜封装双玻组件易出现PVB胶膜部分未熔现象,但加工温度提高又易导致组件冷却缓慢,造成外观发雾模糊现象;在层压温度不超过155℃时,使用双玻组件用EVA胶膜封装双玻组件,外观效果良好。
双玻组件在层压过程比常规晶硅组件更容易出现的缺胶、气泡及移位等缺陷,主要有两方面原因:
1)钢化玻璃在层压机内抽真空阶段受热状态下出现一定程度的翘曲,进入加压阶段时,组件叠层内EVA胶膜受硅胶板压力不均匀,导致EVA胶膜流动不均,影响填充效果,容易出现电池片移位或局部缺胶现象。
2)双玻组件正反两面均为钢化玻璃,玻璃材质的刚性特性以及重量,使得叠层内电池串与电池串之间,玻璃与EVA胶膜之间的空隙所存在的气泡不易在抽真空阶段排尽而产生气泡。
常规组件用EVA胶膜用于双玻组件封装时,因其自身材料性能的局限性,在层压过程中,受钢化玻璃自身重力、抽真空作用力以及硅胶板下压压力的影响,易导致组件内部电池片位移或组件缺胶;温度较高时,因EVA胶膜内部引发剂反应速度过快而产生气泡。
PVB胶膜熔点较高,层压温度较低时,易导致PVB胶膜部分未熔;层压温度较高时,组件冷却缓慢,导致PVB胶膜结晶而使得组件外观模糊。
双玻组件用EVA胶膜通过功能树脂改性,拓宽了层压工艺适用范围,优化了其用于双玻组件加工适应性。
一方面,在抽真空阶段,通过调整抽真空时间,双玻组件用EVA胶膜能够有效地避免电池片位移;另一方面,在加压固化阶段,通过调整层压压力及保持时间,双玻组件用EVA胶膜能够更有效地填充玻璃与电池片、电池片与电池片之间的空隙而避免组件产生缺胶或气泡。
通过制备双玻太阳能组件专用EVA胶膜,同时将其与常规组件用EVA胶膜及PVB胶膜进行封装工艺及效果对比研究表明:
(1) 采用功能树脂改性方法制备的双玻太阳能组件专用EVA胶膜,能更好地适用于双玻光伏组件的封装,能有效避免双玻组件封装过程出现气泡、移位及缺胶等缺陷。
参考资料:双玻组件用 EVA 胶膜的制备及封装工艺研究
END
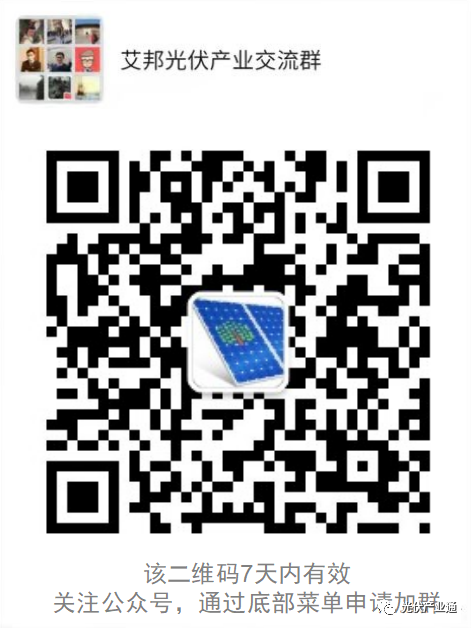
推荐阅读:
原文始发于微信公众号(光伏产业通):双玻组件用 EVA 胶膜的制备及封装工艺研究
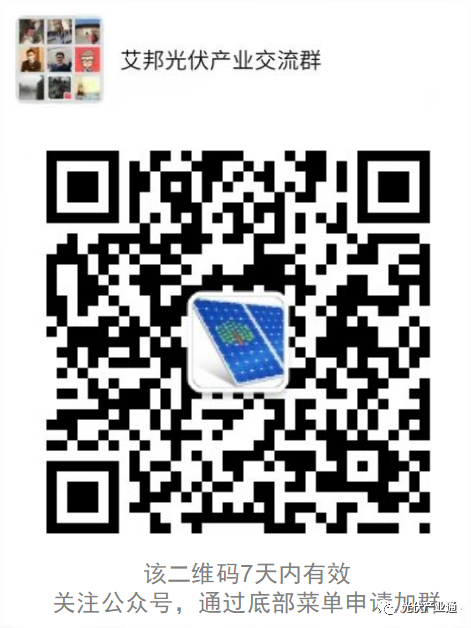