CVD是Chemical Vapor Deposition的简称,是指高温下的气相反应。
例如,金属卤化物、有机金属、碳氢化合物等的热分解,氢还原或使它的混合气体在高温下发生化学反应以析出金属、氧化物、碳化物等无机材料的方法,这种技术zui初是作为涂层的手段而开发的。
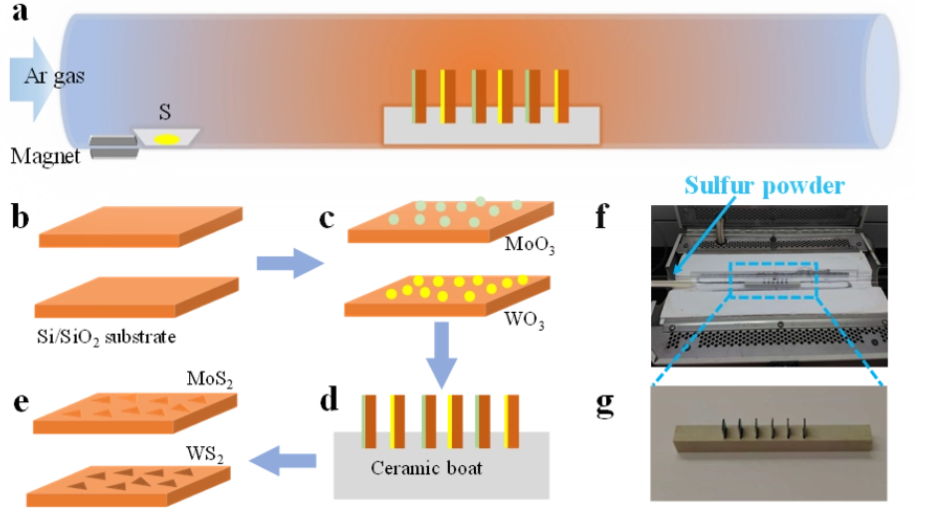
CVD工艺的技术特征:
-
-
析出物质的形态在单晶、多晶、晶须、粉末、薄膜等多种。
-
不仅可以在基片上进行涂层,而且可以在粉体表面涂层等等。特别是在低温下可以合成高熔点物质,在节能方面做出了贡献,作为一种新技术是大有前途的。
在涂层技术的发展中,高温和中温CVD涂层技术是基本的,在多层或纳米涂层中,可通过添加不同金属和涂层微观结构改性来改变涂层性能。
由于CVD为高温工艺,可增强所有扩散及冶金工艺,因此所有涂层特性取决于基体材料。CVD涂层工艺成功应用的第三个关键因素是必须得有工业化的生产设备及生产工艺。这包括在很短响应时间内实现自动工艺控制(如纳米结构)以及可精确控制前驱物质的各源。
现今钙钛矿电池的投资火热,但是距离规模化应用仍具有较大距离。在钙钛矿太阳能电池的性能和成本优势尚未完全实现的同时,硅基太阳能电池的效率不断提高,成本不断下降。钙钛矿太阳能电池能否战胜强大的晶硅,仍需要时间进行验证。设备方面,镀膜设备、涂布设备、激光设备、封装设备为钙钛矿电池制备四大设备,欢迎大家加入艾邦钙钛矿产业链上下游交流群。
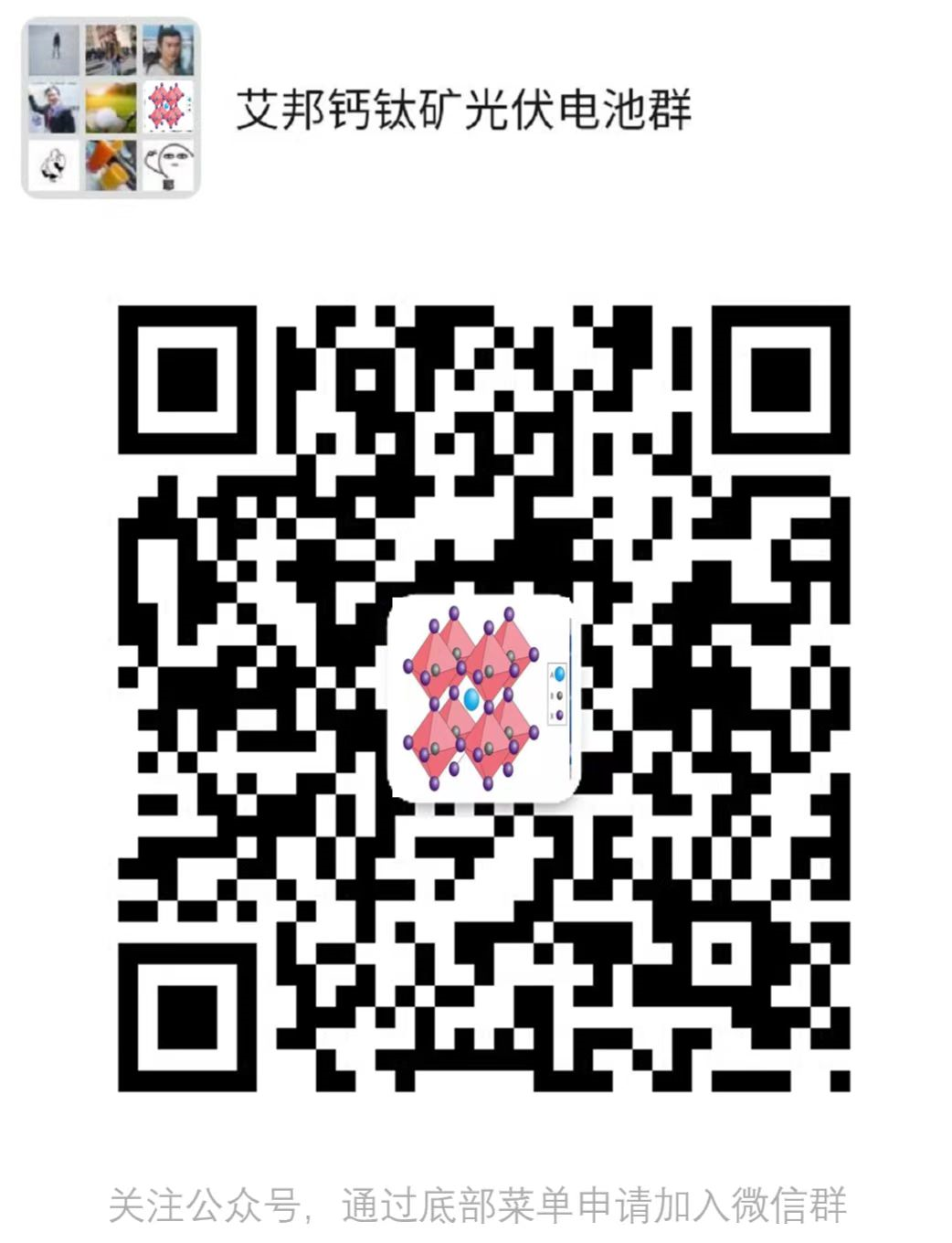
含铬和钒的硬质合金有很高的硬度及一定的韧性,其热膨胀系数接近钢。使用这些材料沉积扩散涂层可获得非常好的结合力。
工业CVD工艺在中温下,在油淬的碳钢制零部件上沉积硬质涂层,某些情况下会产生不一致的结合力。通过含Cr或V的扩散过渡层,工艺和结合力可得到很好的控制。图1展示了结合力较差的涂层(见图1a)和通过Cr扩散涂层获得的结合力较好的涂层(见图1b)。
图1 MT-TiCN在碳钢零件上获得的较差结合力和通过扩散涂层而改进的结合力
这些复合涂层的实现需要额外的前驱物质及设施用于沉积工艺。在上例中,需要额外的发生器来产生挥发性的含Cr化合物——CrClx[2]。在此发生器中,不同的金属(粒状或碎屑状)与氯气或氯化氢进行反应。而此发生器的使用不应将最终的Cr或V残留物带入到后序的涂层中(如氧化铝)。
使用带内部金属氯化物发生器的同一CVD设备,可沉积带掺杂的CVD涂层,通过加入一定量的一种或几种合金(如铬、钒、钨或铊)来改善TiN,TiC或Ti(C,N)涂层性能。
形成的涂层一般为(Ti100-a-b-cCraVbWc)CxNyOz,其中x+y+z=1,其机械性能(如硬度及韧性)与TiN,TiC和Ti(C,N)类似,但由于合金元素的存在,其抗腐蚀性能也得到改善。
从早期的研究[3]可知,在中温Ti(C,N)中添加硼可改变Ti(C,N)典型的柱状结构,获得相当高的硬度。在实际应用中,由于其较高的内部应力及脆性,这种涂层仅限于非常薄的涂层。
因此,通过改变多层CVD涂层的结构,从微米级到纳米级,从而改善涂层性能的研究已经展开。在短暂时间内实现精确控制三氯化硼的流量可获得此纳米涂层。
单一涂层厚度从30nm到60nm的可重复多层涂层已经可进行沉积,在保持纳米结构情况下,总涂层厚度最高可达到10μm。CVD沉积的纳米涂层SEM扫描电镜照片见图2。
沉积非常厚的涂层时,通常晶粒会变得粗大,表面会变得粗糙。这会降低刀具的使用寿命,涂层后抛光处理成本会有所增加。通过掺杂硼来改变结构,可获得非常光滑和光亮的表面。图3和图4展示了单纯沉积MT-TiCN涂层和通过改变多层涂层结构而改进结构和表面形貌的对比(总涂层厚度最厚60μm)。
图4 MT-TiCN多层涂层断面及表面形貌
除了硼,还研究了硫和氧对晶粒细化的影响。图5显示硫仅有稍微的影响,氧和硼可产生显著的晶粒细化效果及表面光滑效果。
高温改性氧化铝应该是防护涂层中应用最成功的抗氧化材料。常见的应用是在硬质合金切削刀片上的氧化铝涂层。
不同金属基体材料和真正陶瓷涂层之间良好的结合力仅能通过使用过渡层来获得,此过渡层可实现以下功能:
催化效应在实际应用中至关重要。含高Co和Cr的合金可用作医疗植入部件材料,这些合金展示了良好的生物兼容性和高机械强度,但是,摩擦性能并不理想,微小的磨损毛刺会产生有害的金属离子。
另一方面,块状氧化铝植入件已在医疗领域广泛应用,但在抗冲击强度和复杂外形成形方面仍有一定的局限性。
在Ti(C,N)和常规氧化铝涂层沉积过渡层可获得较好的机械性能和涂层表面形貌,但Ti(C,N)-Al2O3过渡层易于结合失效。
如图6所示,可重复生产的涂层仅能在齿状过渡层上获得,齿状过渡层能增大内部扩散面积并作为诸如机械互锁增加结合力。
图6 Co基合金上多层涂层(可看到齿状过渡层)的Al2O3扫描电镜照片
相对于上述涂层系统,一些难熔合金(如铌、钽)能直接在其表面沉积氧化铝硬质涂层(见图7)。这为在含钛过渡层为最薄弱环节的抗氧化性高温应用领域开启了新的应用。和硬质合金刀片的氧化铝涂层类似,此类涂层也需要对表面进行一定的特殊改性来获得理想的氧化铝结构(α或κ)。
当有合适的工业涂层设备时,上述所有工艺才能实现成功稳定的生产。总之设备的使用者要求:
针对化学和热处理工艺过程,CVD设备设计的关键因素如下:
物质平衡:热动力学决定了反应发生的条件。不同的涂层工艺,需要有一定量的前驱物。
显然,在一个有数平方米表面的大型成型模具上涂层和在一个有数平方米内表面的过滤器上涂层是不同的。前驱物,室温下的液体可使用现代化的液体质量流量计而达到几乎无限的体积量。
特别是低气相压的氯化物不仅需要较高的反应器温度,而且必须工作在可控负压下以获得足够高的金属氯化物浓度(见图8)。
图8 使用氯气作为氯化反应物的NbCl5发生器,工作在独立压力下的可控沉积工艺
进入系统的前驱物数量也决定了副产品的量或过多的前驱物。传质可控CVD反应会与过多的前驱物一同工作以便在整个反应器内维持理想的涂层均匀性。
这会产生废物管理,即副产品的处理,应不致使下游的泵系统和压力调节装置堵塞。通常的方式是使用高效的冷凝捕捉器(见图9)。
动力学:确保整个反应器内涂层均匀性的最有效方法是改变停留时间(即物质经过经加热的沉积区的停留时间)。
例如,短的停留时间可通过缩短反应器内距离实现,如带中央旋转进气系统在管状反应器内,其停留时间可缩短5个因子。或在低压下进行沉积工艺,不同的真空系统,停留时间可减少10-1000个因子。
低压的额外优点是气体分子的自由程在低压下会增加,从而可提高盲孔和小开孔内涂层的均匀性以及更复杂刀具形状涂层的能力。
热平衡:温度的均匀性也非常重要。反应器和需要涂层的零件的控制温度通常是已知和可控的,主要的影响是工艺气体的温度很难测量,理想状态下,进入的气体直至未排放反应物仍保持低温,仅在距需要涂层的零件很短的距离内达到其反应温度。
显然,新一代的CVD工艺需要通过精确的多样性工艺控制系统在较短的响应时间内进行管理。
CVD设备不同应用(如扩散涂层,掺杂元素,多层涂层系统到纳米涂层)已经实现,设备革新和涂层参数控制的重要性已经显现,以便沉积所需厚度和性能的涂层。工艺开发、过程控制和符合工业要求的工业化设备需要大规模的投资及工程资源。
原文始发于微信公众号(光伏产业通):CVD工艺及设备技术