光伏背板是位于光伏组件背面,对电池片起保护和支撑作用的重要材料,其性能好坏对光伏组件的性能以及使用寿命影响很大。为了保证光伏组件长期可靠性和耐久性,背板应具备卓越的耐候性、电气绝缘性、水蒸气阻隔性等。
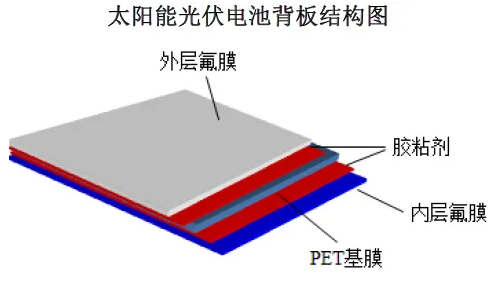
从20世纪80年代光伏组件的封装结构定型以来,以杜邦公司的“Tedlar”聚氟乙烯薄膜(PVF)和PET经过复合成型的PVF/PET/PVF(简称TPT)背板成为光伏背板的首选。
由于PVF薄膜供应限制,3M、阿科玛、苏威等公司开发出了替代产品,如聚偏氟乙烯膜(PVDF)。
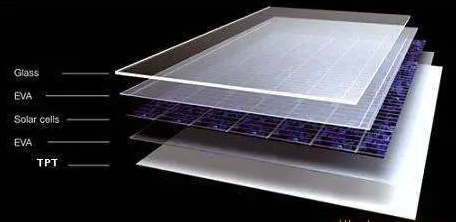
但是以其他氟膜制备的复合型含氟背板与TPT背板类似,基本都是由氟膜/胶粘剂/PET/胶粘剂/氟膜5层结构,其中胶粘剂和PET由于自身分子构成的原因,常常存在耐湿热老化、耐紫外老化性能差的缺点,成为背板的薄弱环节,导致背板在使用时发生脱层、气泡,从而导致电池片脱落、移位,电池有效输出功率下降,严重时甚至导致组件发生火灾。
针对以上问题,我国研究人员开展了用氟涂料制备涂覆型含氟背板的研究,中来、乐凯等公司都有相关产品面市。
由于涂覆型含氟背板面市时间还很短,其对复合型含氟背板在实际使用中的替代性特别是关键性能耐候性的对比研究较少,虽然有将紫外与湿热老化进行结合的实验室快速对比方法报道,但是其并未对背板材料进行明确说明,供业内直接参考的可能性较小。
本研究采用光伏行业常用的紫外、湿热、HAST实验,着重对自制涂覆型含氟背板(背板A)、市售复合型TPT含氟背板(背板B)、市售涂覆型含氟背板(背板C)的耐候性进行对比研究。
表1 实验用背板样品
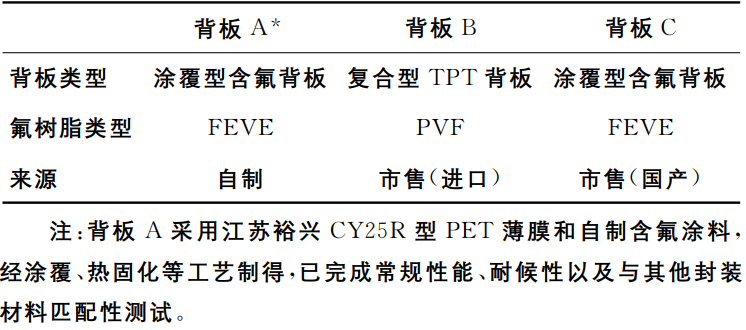
紫外光老化试验机(LRHS-UVN),上海林频仪器股份有限公司;紫外辐照计(UVMETEr),德国WAldMANN公司;湿热老化试验箱(DN-54),百年测试设备(东莞)有限公司;高加速湿热试验机(PC-422R8),日本HIrAYAMA公司;台式色差计(SC-80C),北京康光仪器有限公司;电子扫描显微镜(ΣIGMAHV-01-043),德国CArlZEISSSMT。
根据IEC61215中10.13的要求,温度(85±2)℃、相对湿度(85±5)%。
根据IEC61215中10.10的要求,温度(60±5)℃,波长280~385NM的辐照量≥15KWH/M2,其中,波长280~320NM的辐照量≥5KWH/M2。
截面样品的制样方法为切割,断面喷金150S;扫秒加速电压为20KV。表面样品直接在表面喷金150S;扫秒加速电压为30KV。
按ASTMD3359—08规定进行,在百格刀划格后,再用3M600测试胶带进行粘贴测试,根据涂层剥离程度进行等级判断。
一般来说,黄变指数变化值ΔYI越大,说明材料耐环境老化性能越差。紫外后背板黄变指数变化见表2。
表2 紫外老化后背板黄变指数变化
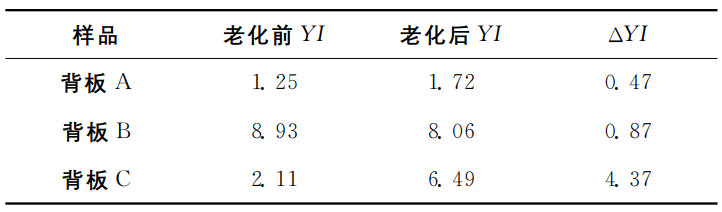
从表2可以看出,经过紫外光辐照,背板A的ΔYI(0.47)最小,背板C的ΔYI最大(4.37),并且超过3。背板A和背板C的黄变指数在老化后变大,背板B反之(与湿热老化后现象一致,下文一同分析)。
根据GB/T31034—2014,复合型背板的层间附着力采用GB/T2790—1995,而涂覆型背板采用GB/T9286—1998。在本研究中,为了直观地将复合型背板和涂覆型背板进行对比,采用ASTMD3359—08标准。紫外老化后,背板的层间附着力变化见表3。
表3 紫外老化后背板层间附着力变化
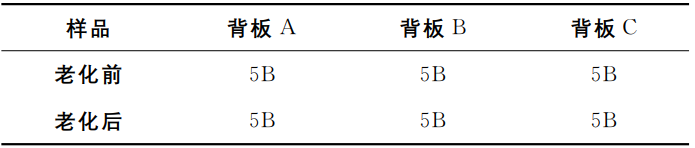
可以看出,经紫外老化后,3种背板的层间附着力都没有明显变化。
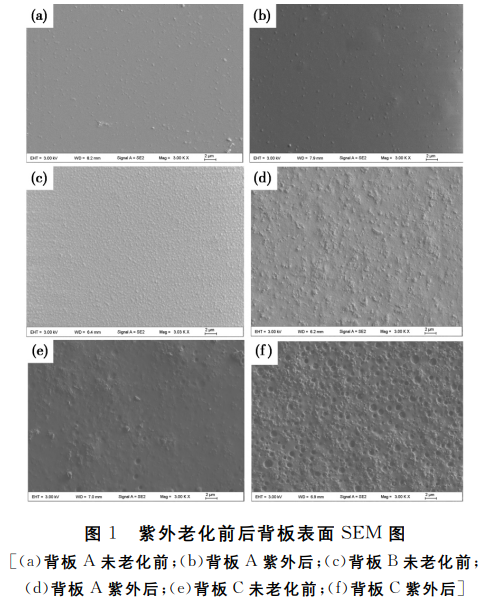
从图中可以看出,经过紫外老化后,背板A表面变化不大,背板B表面颗粒变多、粒径增大,背板C表面凹坑变多。
这可能是背板A采用的FEVE树脂,是氟烯烃和烷基乙烯基醚共聚得到的氟碳树脂,其C—F键能很强,而且氟碳树脂结构交替,氟乙烯结构单元保护了易氧化的乙烯基结构单元,因此,背板A的耐紫外老化性能优异。
背板B的PVF膜在拉伸工艺中,使用较多的助剂,经紫外老化后,助剂发生分解、挥发等改变,造成氟膜收缩、表面塌陷,导致膜中的颜填料等颗粒凸出膜面。
背板C所用的FEVE树脂可能氟原子含量较少,树脂结构不够规整,导致其比背板A更易遭紫外光破坏。
背板黄变指数变化值ΔYI随湿热老化时间的变化见图2。
图2 背板黄变指数变化值ΔYI随湿热老化时间的变化图
从图2可以看出,背板A、背板C的ΔYI随着湿热时间延长而增大。背板B随着时间延长而减小。
这和张晓东等的研究一致,他们认为是湿热环境应力促使TPT背板中的TIO2向表面迁移析出,导致背板黄变指数降低,而TIO2的迁移析出速度先大后小,导致黄变指数变化值也是先大后小。
我们认为,背板B中包裹TIO2的氟膜发生了收缩、粉化及部分脱落等变化,导致TIO2等颗粒状的无机颜填料大量裸露,而TIO2的白度很高,从而使YI比老化前更小(紫外老化后的现象一致)。
ΔYI随着湿热老化的进行逐渐减小的原因,可能是氟膜的收缩、粉化脱落等进程先快后慢,随着时间延长,树脂YI增大,导致整体ΔYI减小。
湿热1000H时,背板A的ΔYI最小(2.25),背板C次之(3.4)、背板B最大(3.8)。2000H时,背板C最大(5.89),背板B次之(3.5),背板A最小(3.12)。在2000H内,背板A的耐湿热老化黄变性能优于背板B、背板C。
在湿热老化1000H及2000H后,背板的层间附着力见表4。
表4 湿热老化前后背板层间附着力变化
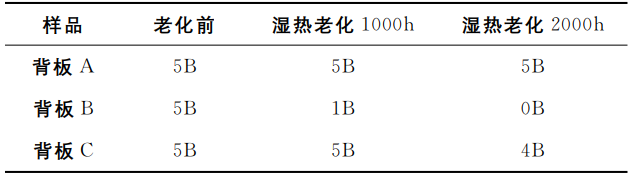
从表4中可以看出,湿热1000H,背板A、背板C的层间附着力仍为5B,背板B则降至1B。
湿热2000H,背板A仍为5B,背板C划格边缘有些许脱落,附着力降至4B,背板B脱落面积很大,附着力降至0B。这主要是背板B的胶粘层经湿热老化后,附着力降低明显,这也正是复合型含氟背板的弊病之一。
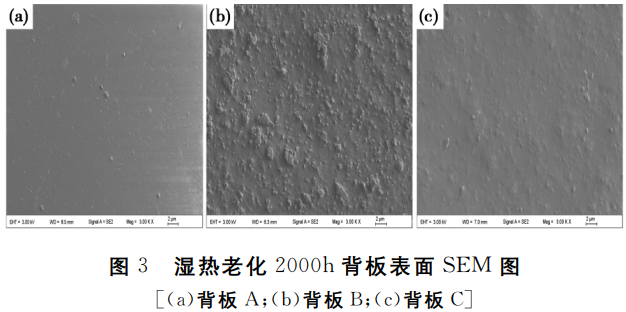
对比图3(A)和图1(A),湿热老化2000H,背板A表面变化不大。对比图3(B)和图1(C),背板B表面颗粒增多、平整度大大下降。
这可能是背板B中的助剂发生挥发、流失、分解等变化,造成氟膜收缩、表面塌陷,导致膜中的颜填料等颗粒凸出膜面。对比图3(C)、图1(E)、图1(F),可以看出背板C对紫外光更敏感,而温湿度对其的影响稍弱。
无论是复合型还是涂覆型含氟背板,表层氟树脂耐候性都比较强,背板耐候的薄弱部分主要是PET以及PET和含氟层的结合层(复合型)。因此又考察了老化后背板截面微观变化(见图4)。
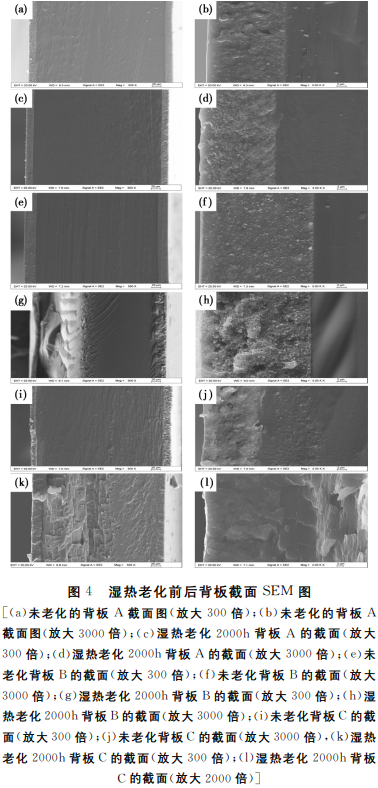
对比图4(A)、图4(B)、图4(C)、图4(d),湿热2000H,背板A的含氟层-PET-含氟层结构紧密,含氟层结构致密、颗粒分散均匀,PET层没有出现脆裂等情况。
对比图4(E)、图4(F)、图4(G)、图4(H),老化后背板B含氟层出现明显脱层,PET发生脆裂,含氟层内部出现很多孔隙。对比图4(I)、图4(J)、图4(K)、图4(l),背板C在湿热后,虽然含氟层变化不明显,也没有发生明显脱层,但是PET也出现脆裂,这主要是PET在湿热老化条件下发生水解。
表5 HAST 48H背板黄变指数变化
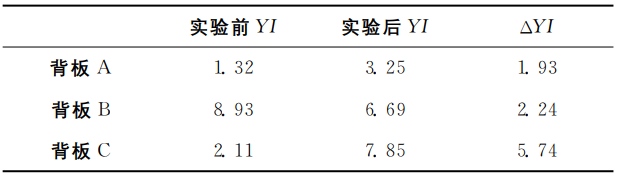
从上表可以看出,背板A的耐黄变性能最好,背板C的最差。背板B的黄变指数也在HAST后的变小,和紫外、湿热老化实验中的规律一致。
表6 HAST 48H背板层间附着力变化
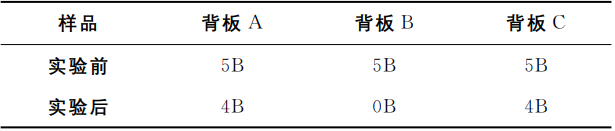
从表6可以看出,HAST48H后,背板层间附着力都有下降,其中背板A和背板C下降较少,背板B下降最大,而且背板B的PET层有明显粉化现象。HAST比双85湿热更苛刻,因此对PET的水解进一步增强,背板性能降低也更明显。
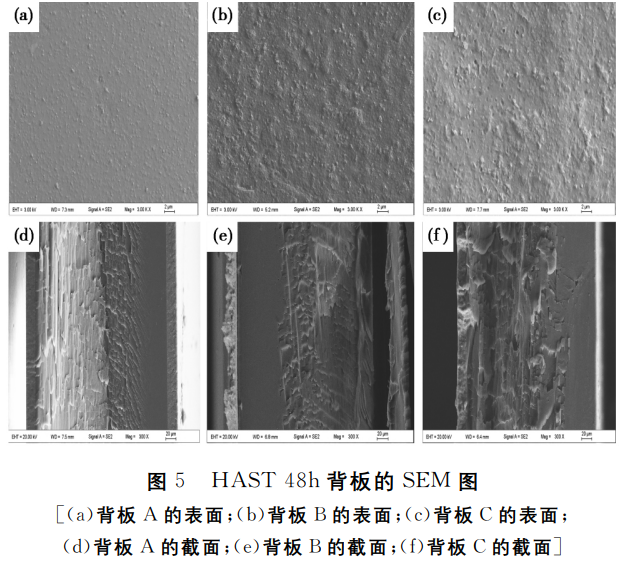
对比图5(A)和图1(A)、图5(B)和图1(C)、图5(C)和图1(E),3种背板在HAST后表面颗粒增多,其中背板B和背板C颗粒明显增多,背板C的表面有明显凹坑。
对比图5(A)和图4(A),图5(B)和图4(E),图5(C)和图4(I),3种背板在HAST后,PET都出现了脆裂,背板B还出现了明显脱层。
紫外老化后,背板的层间附着力基本无变化;背板A的ΔYI最小,背板C最大;SEM表明,背板B表面颗粒数量增多、粒径增大,背板C表面出现凹坑。
背板A、背板C的ΔYI随湿热时间延长而增大,背板B反之;在2000H内,背板A的耐湿热黄变性能优于背板B、背板C。SEM表明,背板B表面颗粒增多,含氟层和PET出现脱层,PET发生脆裂。背板C的PET也出现脆裂。
HAST48H,背板A的耐黄变性能最好,背板C最差。层间附着力背板A和背板C下降较少,背板B下降最大,而且背板B的PET层有明显脆裂粉化现象。SEM表明背板B颗粒数量明显增多、明显脱层,背板C表面出现颗粒、气孔。3种背板PET层都出现了脆裂。
原文始发于微信公众号(光伏产业通):含氟光伏背板耐候性研究